News Story
Researchers’ Battery Breakthrough Improves Performance at Lower Costs
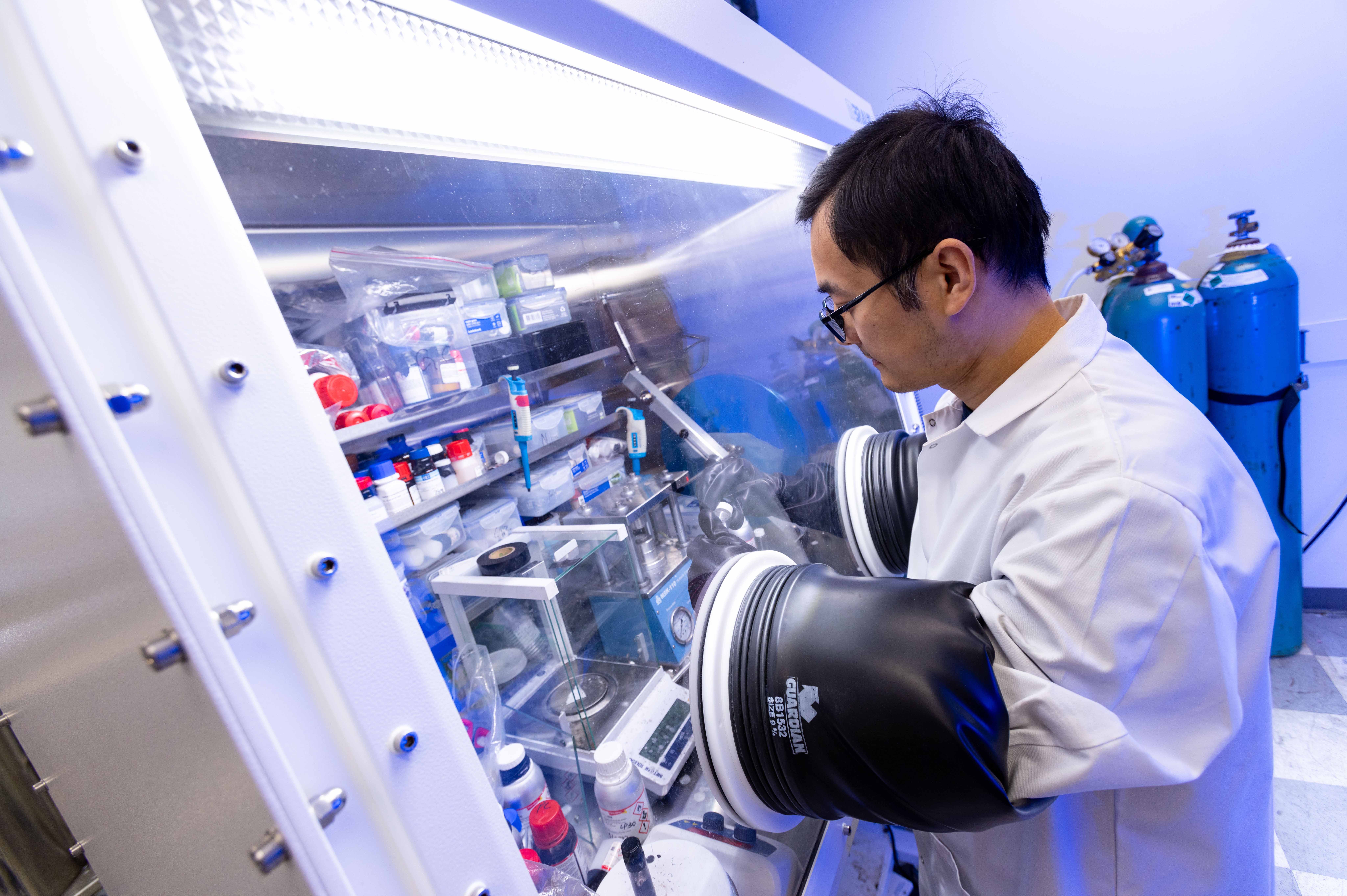
Li using a glovebox to prepare the electrolytes inside Wang's laboratory. Photography by John T. Consoli.
Researchers aiming to boost capabilities in modern batteries used in consumer products and vehicles have designed a new technology with improved performance and lower manufacturing costs.
Battery expert Chunsheng Wang, a professor in the Department of Chemical and Biomolecular Engineering, broke through some of the challenges preventing a new wave of modern batteries leveraging low-cost, large-sized silicon materials. The new technology, which comes at higher energy efficiency and reduced environmental and manufacturing costs, was proposed in a Nature Energy paper published today.
Efforts to roll out new lithium-ion batteries that incorporate silicon materials are underway as these devices are poised to come with higher energy capabilities and lower costs due to the large natural abundance of silicon in the environment. But before the new batteries can hit the market, researchers are studying ways to make them work in large-sized alloy particles, which can further reduce the cost.
A key component that allows continuous charge and discharge cycles of the batteries, called the electrolytes, currently lacks the capability to stabilize the high energy of alloying anodes, causing them to fail, or short circuit. To address this challenge, Wang’s research team designed a series of new electrolytes that enables the successful operation of lithium-ion batteries using micro-sized alloying anodes (silicon, aluminum, tin, and bismuth).
“Our research suggests a practical electrolyte recipe that can be used to stably cycle micro-sized silicon particles, which has been regarded as unachievable before,” said CHBE Assistant Research Scientist Ai-Min Li, first author of the study.
They accomplished this design by using asymmetric molecular design, which makes the derivatives of a widely employed ether solvent in battery research, called “dimethoxyethane,” compatible with commercial lithium hexafluorophosphate salt. This design enabled the long-cycle performance of micro-sized alloying anodes and removed environmental concerns associated with fluorinated solvents used in modern batteries.
Their work enabled a cost-effective technology that requires simpler and fewer manufacturing processes associated with the nano-sized silicon materials, allowing for widespread adoption. Moving forward, the researchers aim to patent their invention and commercialize it via Wang’s venture, WH-Power, a battery manufacturing company that he co-founded with Associate Dean of Research Robert Briber and Visiting Research Professor Liangbing Hu.
Their work was supported by a grant to develop lithium-ion batteries that meet the United States Advanced Battery Consortium, a cooperative agreement between the Department of Energy and the United States Council for Automotive Research targeting operating environment conditions, fast charge capability, and calendar life testing for next-generation batteries.
Published August 20, 2024