News Story
Researchers Work to Develop Custom Conformal N95 Respirators
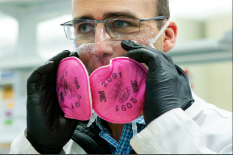
Kevin Aroom
Researchers across the University of Maryland's Robert E. Fischell Institute for Biomedical Devices and A. James Clark School of Engineering are working tirelessly to address the critical supply of N95 respirators – commonly referred to as N95 masks – to protect health care workers and their patients on the front lines of the COVID-19 pandemic.
Single-use N95 respirators – first developed by 3M – are different from standard surgical masks in that they are designed to filter up to 95% of airborne particles such as viruses from the air. Even more, 3M respirators also apply an electrostatic charge to the material to further prevent incredibly small particles from making their way through the mask fibers. The longer a caregiver or patient wears the N95 respirator, the more likely it is that it will become ineffective. In addition, nurses wearing the same mask for lengthy hours have experienced significant facial bruising. Given this experience, N95-rated respirators that can be cleaned and safely reused are in high demand as hospitals and physician’s offices continue to work through their supplies.
To address this critical need, Fischell Institute researchers are working in close collaboration with clinicians, faculty, and staff across the University of Maryland, College Park (UMD) and Baltimore (UMB) campuses, as well as with Walter Reed National Military Medical Center, Washington Hospital Center, and Children’s National Medical Center to develop solutions that will keep both doctors and patients safe as demand for masks continues to rise.
Fischell Institute director William E. Bentley, faculty member Lex Schultheis, and engineer Kevin Aroom are leading the University of Maryland’s charge to develop a prototype of a reusable mask that can be personalized to fit the contours of an individual’s face. With the help of input from other institutions and dozens of area engineers – including UMD Unmanned Aircraft Systems Test Site Director Matthew Scassero – and clinicians – including UMB’s Joseph R. Scalea, M.D. – Aroom has logged long hours in the Fischell Institute lab working to design and test 3D-printed molds for conformal masks using facial scanning software and in-house printers, including those in Terrapin Works. In addition to addressing the short supply of N95 respirators, the Fischell Institute team hopes that by offering health care workers a custom-fitted mask, they can create the best possible seal to safeguard against virus particles. In addition, the mask itself could be washed – and the filter portion of the mask replaced – ahead of each new wear, preventing future mask shortages. The filter attaches to the mask using a standard port, which allows users to be more versatile in filter selection. Because the Fischell Institute team plans to 3D print the mask using clear polymers, the wearer’s mouth would be visible – which makes it easier for health care workers to communicate with one another and with their patients in an already stressful environment.
Even more, Clark School engineers are also working to identify alternative or reusable filter materials.
As testing confirms the safety and effectiveness of these approaches, the hope is that the U.S. pipeline of N95 respirator masks could be bolstered by U.S. industry and maker facilities such as UMD’s own Terrapin Works and ActivArmor, a long-time Fischell Institute collaborator that specializes in custom 3D-printed casts and splits.
The Fischell Institute has filed for a U.S. Food and Drug Administration Emergency Use Authorization. Additional updates will be shared as they are made available.
Published March 31, 2020