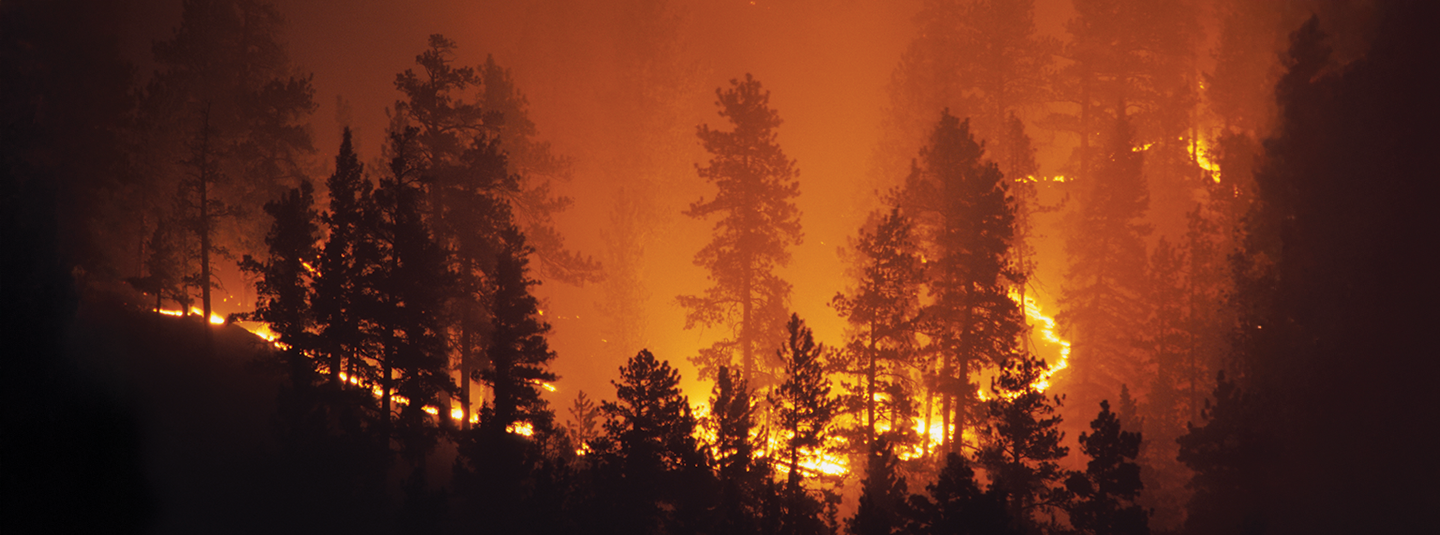
Globally, the severity of wildfires is increasing—they spread faster and burn larger areas at higher intensities. Maryland engineers are developing new, innovative tools to keep up with the increasing threats and mounting challenges posed by extreme wildfire events.
Wildfires can ignite in remote places. But all too often, their destructive fury encroaches on homes and communities. In January 2025 alone, wildfires in California burned more than 57,000 acres, costing 29 lives and destroying more than 16,000 homes and other structures. Maryland engineers are designing drone-based systems for autonomously assessing, and even fighting, fires like these from above.
Two teams are working on separate projects with related goals. The first, funded by a UMD Grand Challenges Grant, aims to develop drones that fire departments could fly over fires to collect information about them in real time, so they can make more informed decisions about how to fight them. The machine’s AI would possess the capacity to navigate along a fire on its own. All the while, it would assess images from its visible light and infrared cameras to identify the burning areas below. This data would be transmitted to the ground, where firefighters could use it to find a fire or modify their strategies for fighting it.
A second team, called Crossfire, is participating in the XPRIZE Wildfire competition, which challenges participants to develop autonomous technology capable of detecting an early-stage wildfire somewhere in a 1,000 square-kilometer area, and then suppressing it (all within 10 minutes). To put out a fire once it’s identified, the team is experimenting with a well-established fire suppressant: water. This task would likely be carried out by a different drone or drones, which would release a water-carrying vessel that ruptures at a predetermined height above the fire.
Ultimately, Fernando Raffan-Montoya, an assistant professor of fire protection engineering leading the first wildfire project and collaborating on Crossfire, envisions systems like these informing on-the-ground decisions, such as when to order evacuations. Drone-based fire suppression, meanwhile, could one day protect communities from an approaching wildfire, he says.
Between climate change, which creates conditions more conducive to fires, and increased building in wildland areas, the problem will continue to grow. “We believe that autonomy will bring a much-needed part of the solution,” Raffan-Montoya says.
Student Spotlight: Help Where Humans Can’t
A drone’s cameras can capture a small fire all at once. But, more often, fires are too big for a single image.
Andrés Felipe Rivas Bolivar, a Ph.D. student in aerospace engineering working on the Grand Challenges wildfire project, is developing an image recognition algorithm to identify the edge of a fire. With this information, the algorithm generates a trajectory along which the drone navigates to capture the fire’s full scope.
Raffan-Montoya recruited Rivas Bolivar from Colombia, where Rivas Bolivar had designed and built drones first as a hobby and then through his master’s program in mechanical engineering. Rivas Bolivar envisions a drone-based monitoring system being used in places, including Colombia, where fire departments may not have the resources to monitor fires with manned aircraft.
“We’re just in the investigation phase now,” Rivas Bolivar says. “But at the end, if we have a platform that does all the things we are thinking of, it could help firefighters save money and lives.”