News Story
TAP Assists in Biofuel Advance
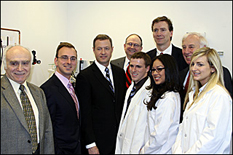
Pictured: (top row, left to right: Herbert Rabin, acting dean, A. James Clark School of Engineering; Scott Laughlin, former director of Mtech's VentureAccelerator Program; Governor Martin O'Malley; Zymetis President and CEO Steve Hutcheson; Steve Davey, Chief Operating Officer of Zymetis; C. Daniel Mote, Jr., University of Maryland President. Bottom row, in lab coats (all recent UM alumni) Dan Forrest; Elizabeth Santos; Kristen Goff.
A chance discovery not detected in the Bay since, the bacterium, called Saccharophagus degradans, can create a mixture of enzymes—through a patent-pending system developed by College of Chemical and Life Sciences Professors Steve Hutcheson and Ron Weiner—that break down almost any source of biomass, or plant life, into sugars, which are then converted into ethanol and other biofuels. Called Ethazyme™, the biomass-degrading enzyme mixture is licensed exclusively to University of Maryland spin-off Zymetis Inc.
Zymetis is the newest company to join the university’s technology company incubator, the Technology Advancement Program (TAP). Zymetis also just entered a partnership with Fiberight, a regional company that processes cellulosic waste products (such as paper not normally collected as part of existing recycling programs). The two companies are teaming to establish by the end of 2008 a full-scale facility to process various cellulosic waste products into ethanol.
Today, ethanol is made primarily from corn. It is used mostly as an additive to gasoline rather than a fuel alternative, due in part to a strong demand for corn by the food industry, according to Hutcheson. Zymetis’ system can make ethanol and other biofuels from many different types of plants and plant waste (cellulosic sources), potentially making it a viable and inexpensive gasoline substitute.
Cellulosic biofuels can come from non-grain plant sources such as waste paper, distillers’ spent grain (brewing byproducts), leftover materials from agriculture—including straw, corncobs and husks—and energy crops such as switchgrass. Biofuels produced from these inexpensive and renewable sources could exert less of a negative impact on the environment than either corn-based ethanol or gasoline.
Because these biofuels can be made entirely in the U.S., their widespread adoption domestically could also reduce the nation’s dependence on foreign oil and potentially secure its energy supply.
“We believe we have the most economical way to make the novel, efficient enzymes needed to produce biofuels from cellulosic material,” says Hutcheson, who is on leave from the university and is founder and CEO of Zymetis. “Ethazyme breaks down cellulosic sources faster and more simply than any product available, resulting in lower costs.”
Cellulosic materials share one challenge—they are tough. The rigidity of plant cell walls forces ethanol producers to soften them with chemicals through a lengthy, multi-step pre-treatment process even before attempting to break them down into biofuel-ready sugars.
Ethazyme™ degrades cell walls and breaks down the entire plant material into sugars in one step, creating fermentable sugars faster and at a significantly lower cost. The need for caustic chemicals used by competing processes is also reduced.
The company’s enzymes are easy to produce, work well in a water-based environment, are active under industrial conditions and rapidly break down plant material—meaning fewer enzymes will be needed to do the work, according to Hutcheson.
An additional challenge, generating improved fuel yields from sugars, is the subject of a new research project Zymetis is conducting with Life Sciences Associate Professor Jonathan Dinman. Dinman is genetically engineering a yeast strain, using genes from the Bay-derived bacterium, to improve the production of ethanol from fermentable sugars by at least a third. The project, worth $112,000, is jointly funded by both the MTECH Maryland Industrial Partnerships (MIPS) Program and the company.
Founded in 2006, Zymetis entered the university’s MTECH VentureAccelerator Program, which provides hands-on business assistance to faculty and students interested in forming companies around university-created technologies. “MTECH VentureAccelerator helped us validate our market,” says Hutcheson. “They found space for our company. They helped us with licensing our technology, forming financial and business plans, and establishing trademarks.”
Zymetis also sought expertise from MTECH’s Bioprocess Scale-Up Facility (BSF) staff to determine how to mass-produce S. degradans. The BSF is part of the MTECH Biotechnology Research and Education Program, an initiative dedicated to research, education and the development of biotechnology products and processes for Maryland companies.
Hutcheson, along with Weiner, won the university’s Office of Technology Commercialization Inventor of the Year Award in 2007 in the Life Science category for his enzyme system invention.
Although Zymetis researchers have been unable to isolate the bacterium in the Bay again, they are producing it in their laboratories through cultured growth.
The energy bill passed by the U.S. Senate on Dec. 13 mandates oil companies to blend in 21 billion gallons of cellulosic ethanol with their gasoline by 2022. Hutcheson projects a $5 billion enzyme market for biofuels.
Published March 11, 2008