News Story
Former MEI2 energy seed grant discusses 3D printing of advanced ceramics
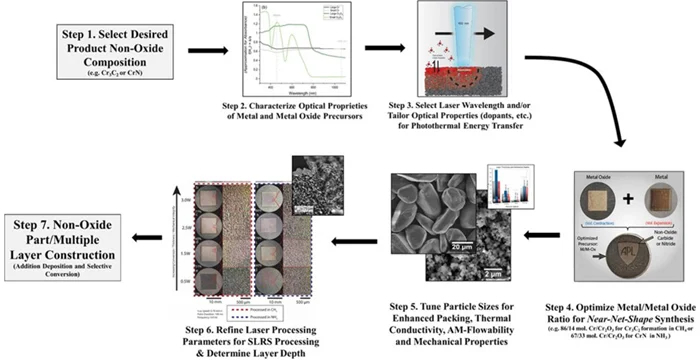
Explaining the SRLS process
Materic was the recipient of a Phase I energy seed grant in 2018 and a Phase II awardee in 2021. Based in Baltimore, Maryland, Materic custom designs and manufactures advanced materials. They apply expertise in electrospinning, nanoparticle separation, textile treatments, 3D printing materials, specialty inks and microencapsulation to their own product lines as well as taking on custom manufacturing projects for customers.
The following story was originally published on October 8, 2024 by Madeleine P.
3D printing has revolutionized many industries thanks to its ability to create complex, customized geometries using a variety of materials. Among these, ceramics have emerged as a very attractive option due to their properties (high wear resistance, thermal stability, corrosion resistance, etc.). In the field of ceramics, carbide and nitride stand out for their superior performance in demanding applications. Integrating these advanced ceramics into 3D printing not only expands industrial manufacturing possibilities, but also opens up a world of possibilities for many cutting-edge sectors, such as energy or defense. In this context, startup Synteris has developed its own additive manufacturing technology to optimize the creation of parts with these materials. We spoke to one of its co-founders to find out more.
3DN: Could you introduce yourself and tell us about your connection with 3D printing?
Ken Malone, I am a Board Chair of Materic and a co-founder of Synteris. I’m a polymer scientist by training and spent the early part of my career working for global polymer and specialty chemical companies with responsibilities including manufacturing, technical support, marketing, business management and M&A. The mid-point of my career was in academic leadership where I had some responsibilities in technology transfer. The combined knowledge of polymers and university innovation led me to co-found a number of companies that custom manufacture advanced materials based on intellectual property licensed from universities. This includes companies with 3D bioprinting, 3D printing of oxide ceramics, a commodity 3D print shop, and Synteris.
3DN: What is Synteris, and how did the idea for the company come about?
Synteris is a subsidiary of Materic, a custom manufacturer of advanced materials in 3D printing, nanomaterials, functional inks, technical textiles, and control release technologies. It was formed to license and commercialize the invention of Adam Peters et al. from Johns Hopkins University. The management of Materic identified Peters’ invention as having substantial synergy with their existing 3D printing developments.
3DN: How does SLRS technology work and what are its main benefits?
Ceramics printed using our Selective Laser Reaction Sintering (SLRS) technology do not require post-processing and have no change in volume of the printed part. This process is able to manufacture parts from ceramic materials such as SiC, Si3N4, AlN, HfC, ZrC, TiC, HfN, ZrN, TiN, TaC, and TaN.
The process to accomplish this is conceptually straightforward, pump a reactive gas such as methane into the chamber while fusing a metal/metalloid such as silicon and the result will be a metal carbide/nitride such as SiC. Mix the right starting powders and the right gas mix and we are able to achieve net shape printing of complex metal carbide and metal matrix composites at full density.
From a less technical perspective, think about that pottery class you took as a kid where you made a big coffee mug, put it into the furnace and it came out 1/3 the size. That shrinkage is what happens with all types of ceramics but it’s what we avoid. We’re the only method out there for making complex ceramic parts with no shrinkage that are also at full density.
3DN: What sectors and applications does this technology target?
Energy, defense, and industrials are the primary sectors we have printed parts for. They include components of rockets, modular nuclear reactors, and power electronics. While very different market applications, they all share a common need for a high temperature material with a complex shape.
3DN: How do you see the future of 3D printing in 10 years? What about Synteris itself?
3D printing has largely entered the transition from new tech where lots of companies are formed each year to chase new ideas to a consolidation phase where the focus is on manufacturing efficiency and scale. There are still some exciting areas for new tech in 3D printing that aren’t going to be a part of that consolidation. In areas such as ceramics, companies like Synteris will continue to launch and bring fresh ideas to the market.
We expect Synteris tech to be well established in ten years but with energy and defense markets there’s a slow adoption curve. These are rightly markets that need to establish strong safety performance of parts before anything goes commercial. In ten years, Synteris will likely be just getting routine manufacturing orders. We’d love it to happen much faster but the rate limiting step will be customer adoption not technology readiness.
3DN: Any last words?
We are open to complex projects involving metal carbide or metal matrix composites. Call us or find more information on our website here.
What do you think of the technology developed by Synteris? Let us know in a comment below or on our LinkedIn, Facebook, and Twitter pages! Don’t forget to sign up for our free weekly newsletter here for the latest 3D printing news straight to your inbox! You can also find all our videos on our YouTube channel.
*All Photo Credits: Synteris
Published October 8, 2024